ERW (Electric Resistance Welded) tubes, also known as electric fusion welded pipes, are a vital component in various industries, from construction to oil and gas, automotive to shipbuilding. These tubes are manufactured through a high-frequency welding process that involves the fusion of metal edges without the need for filler material. The precision and efficiency of this method have made ERW tube factories essential players in global manufacturing.
ERW tube factories are modern marvels of industrial production, equipped with state-of-the-art machinery and technology. The process begins with the selection of high-quality raw steel coils, which are then formed into a tubular shape by a series of rolls. The edges of the formed tube are then brought together and fused by an electric current, creating a seamless weld. This method results in tubes with exceptional strength, uniformity, and a smooth surface finish.
The quality control in these factories is stringent, with rigorous testing procedures carried out at every stage of production. Non-destructive tests like ultrasonic testing, X-ray testing, and eddy current testing ensure the integrity of the weld seam. Furthermore, these factories often adhere to international standards such as API, ASTM, and EN to guarantee their products meet global quality benchmarks.
ERW tube factories also prioritize sustainability and environmental responsibility. They implement energy-efficient practices and recycle waste materials wherever possible They implement energy-efficient practices and recycle waste materials wherever possible
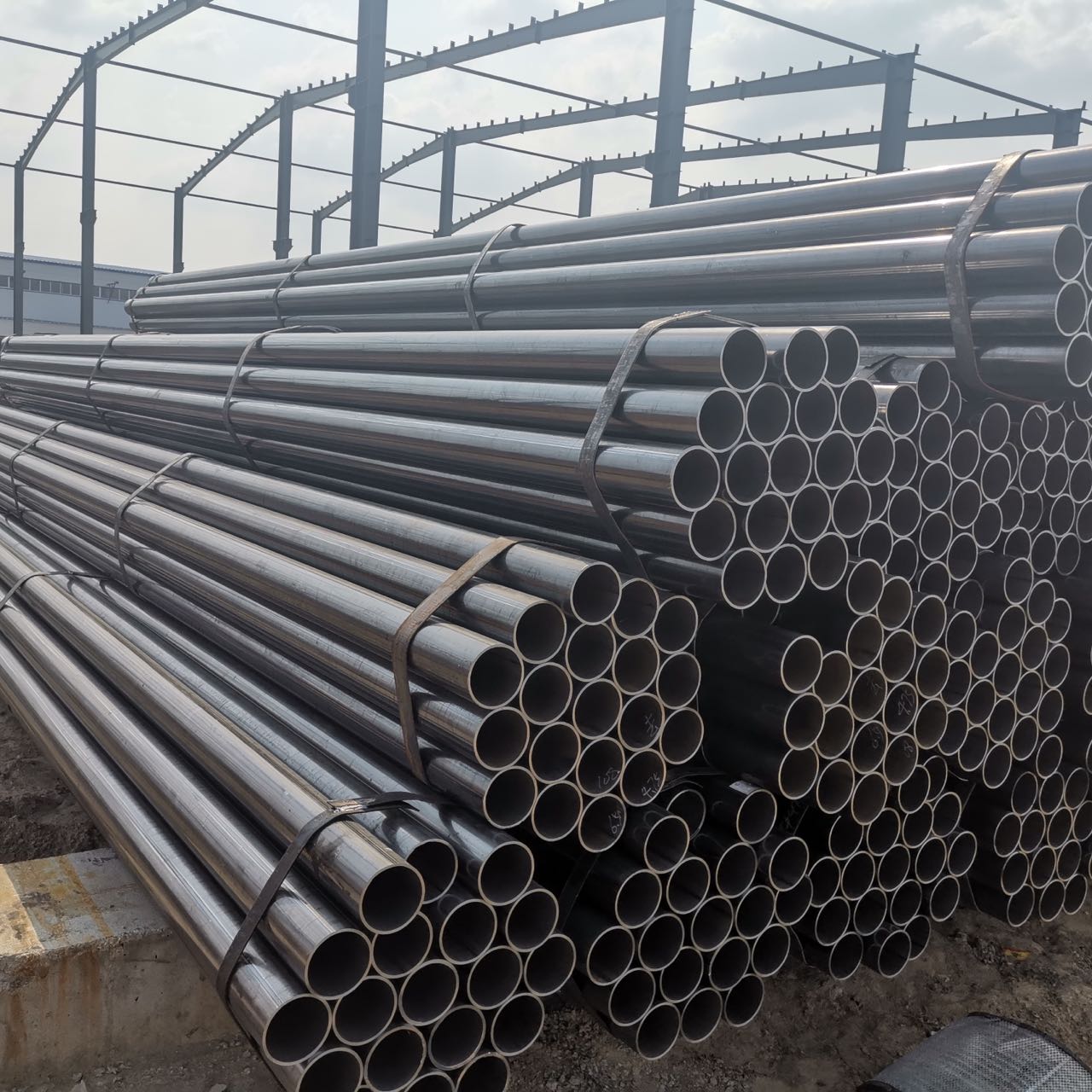
They implement energy-efficient practices and recycle waste materials wherever possible They implement energy-efficient practices and recycle waste materials wherever possible
erw tube factory. The use of advanced technology allows for minimal scrap generation and efficient resource utilization, contributing to a greener manufacturing process.
In recent years, the demand for ERW tubes has been on the rise due to their versatility and cost-effectiveness. They can be customized to meet specific requirements, from small diameter precision tubes to large diameter structural pipes. ERW tube factories have thus become key suppliers to sectors ranging from infrastructure development to high-tech engineering.
The future of ERW tube factories looks promising, with ongoing advancements in automation and digitalization expected to enhance productivity and precision even further. The integration of Industry 4.0 technologies like IoT (Internet of Things), AI (Artificial Intelligence), and robotics is set to revolutionize the manufacturing process, making it more efficient, flexible, and responsive to market demands.
In conclusion, ERW tube factories are not just manufacturing hubs; they are centers of innovation and technological advancement. Their contribution to global industry is significant, providing high-quality, reliable products while constantly adapting to evolving needs and sustainability challenges. As we move towards a more technologically driven future, ERW tube factories will continue to play a pivotal role in shaping the world around us.